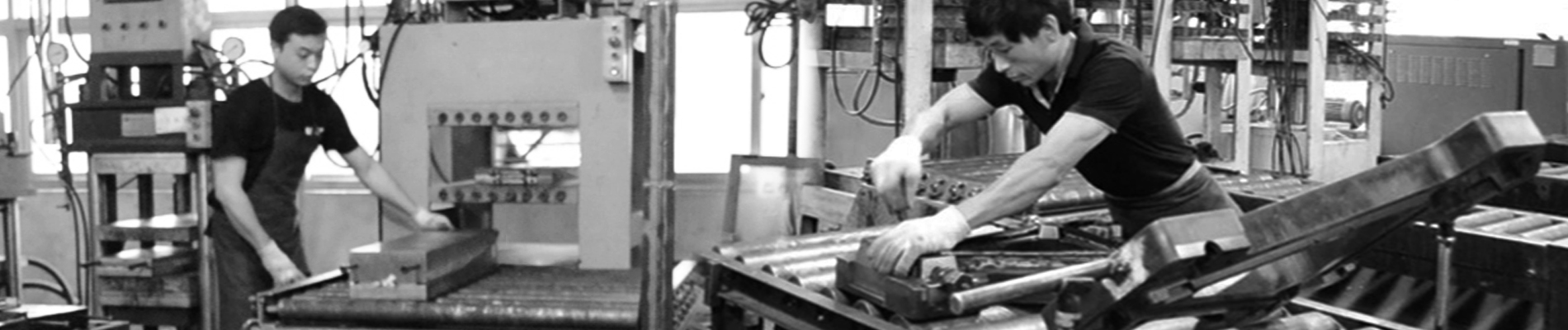
The Production Process of Carbon Rims In TOP-FIRE
The Production Process of Carbon Rims In TOP-FIRE
TOP-FIRE represents the latest technological advances in carbon-fiber bicycle rim performance products. Engineered from the trail up to be lighter, stronger, faster and more aerodynamic.The production processes are as follows:
Preform fit->Preform into the mold->Thermoforming->cooling->Mould to take product->Pull air bag->Secondary heating->Sandblasting->Hole processing->Polish
Preform fit:
Paste the shape of the product according to the structural design drawing, not more paste less paste.
Preform into the mold:
When entering the mold, the preformed product should be straightened out to avoid yarn clamping.
Thermoforming:
155±5℃/1 hour.
cooling:
After cooling, the mold surface temperature is 90℃↓.
Mould to take product:
The product must not be bruised.
Pull air bag:
The air bag needs to be removed clean.
Secondary heating:
The product is heated twice to eliminate internal stress and improve the reaction rate. 150±5℃/2.5 hours.
Sandblasting:
The product is sandblasted and coarsened.
Hole processing:
Choose the correct program for hole processing according to customer needs.
Polish:
Add primer to the surface of the product and make the surface of the product smooth.
Copyright © 2025 Top-Fire Carbon Technology Co., Ltd. All Rights Reserved. Power by
IPv6 network supported